Aerodynamics
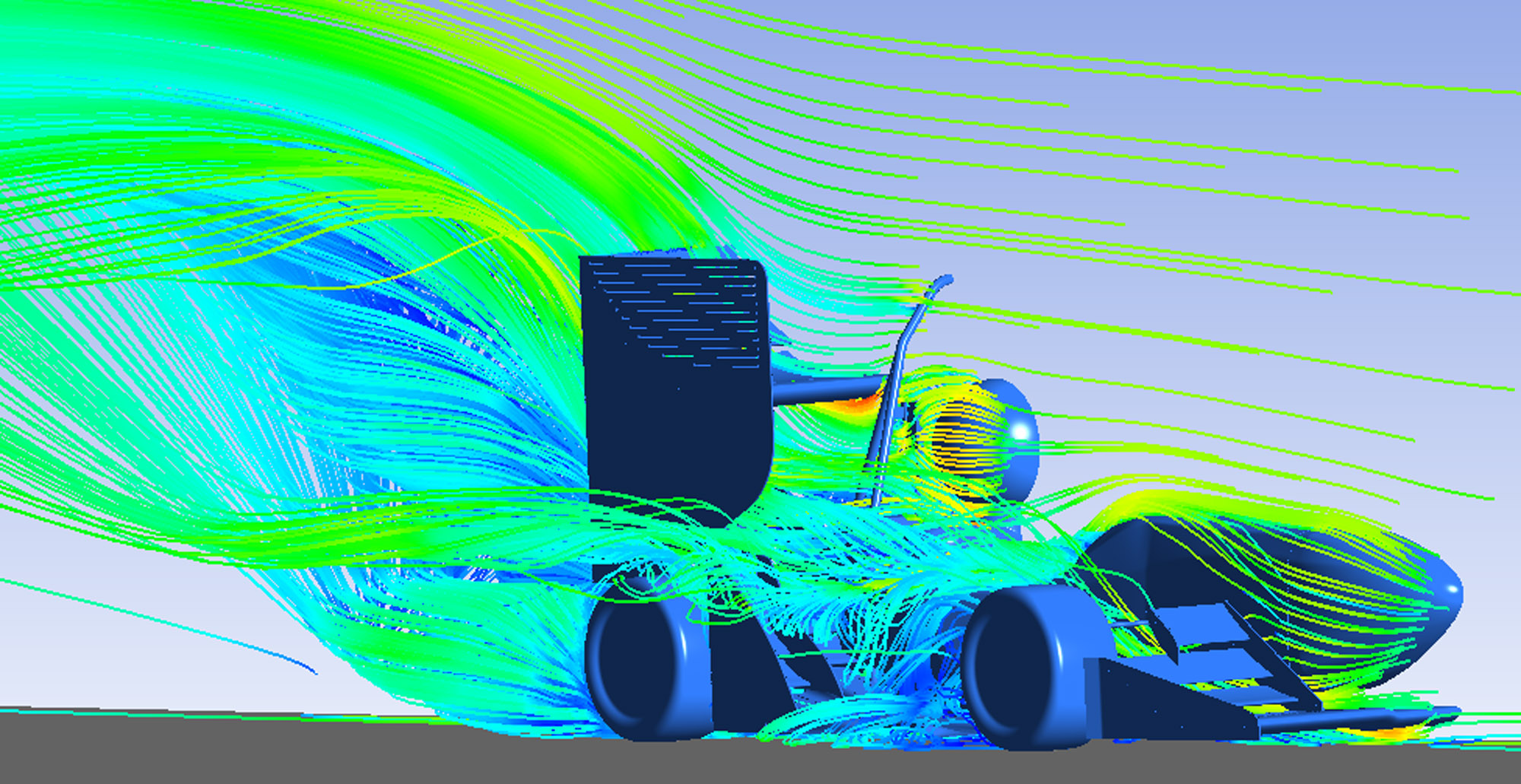
Aerodynamics designs, manufacturers, and tests the aerodynamic package of the car. The package includes a front wing, an undertray (floor), side wings, sidepods, and a rear wing. Using Solidworks and Ansys Computational Fluid Dynamics (CFD), the team designs, tests, and iterates upon their models in the Fall. In the Winter the team works with the Composites team to manufacture the package entirely out of carbon fiber. Once the rest of the car is ready to roll, the Aero team uses tassels and flow-vis to compare simulation results to reality. On test days, the Aero team works with Suspension and Drivers to confirm Aero balance. The downforce generated by the aerodynamics package is crucial to high-speed cornering and overall performance.
Chassis
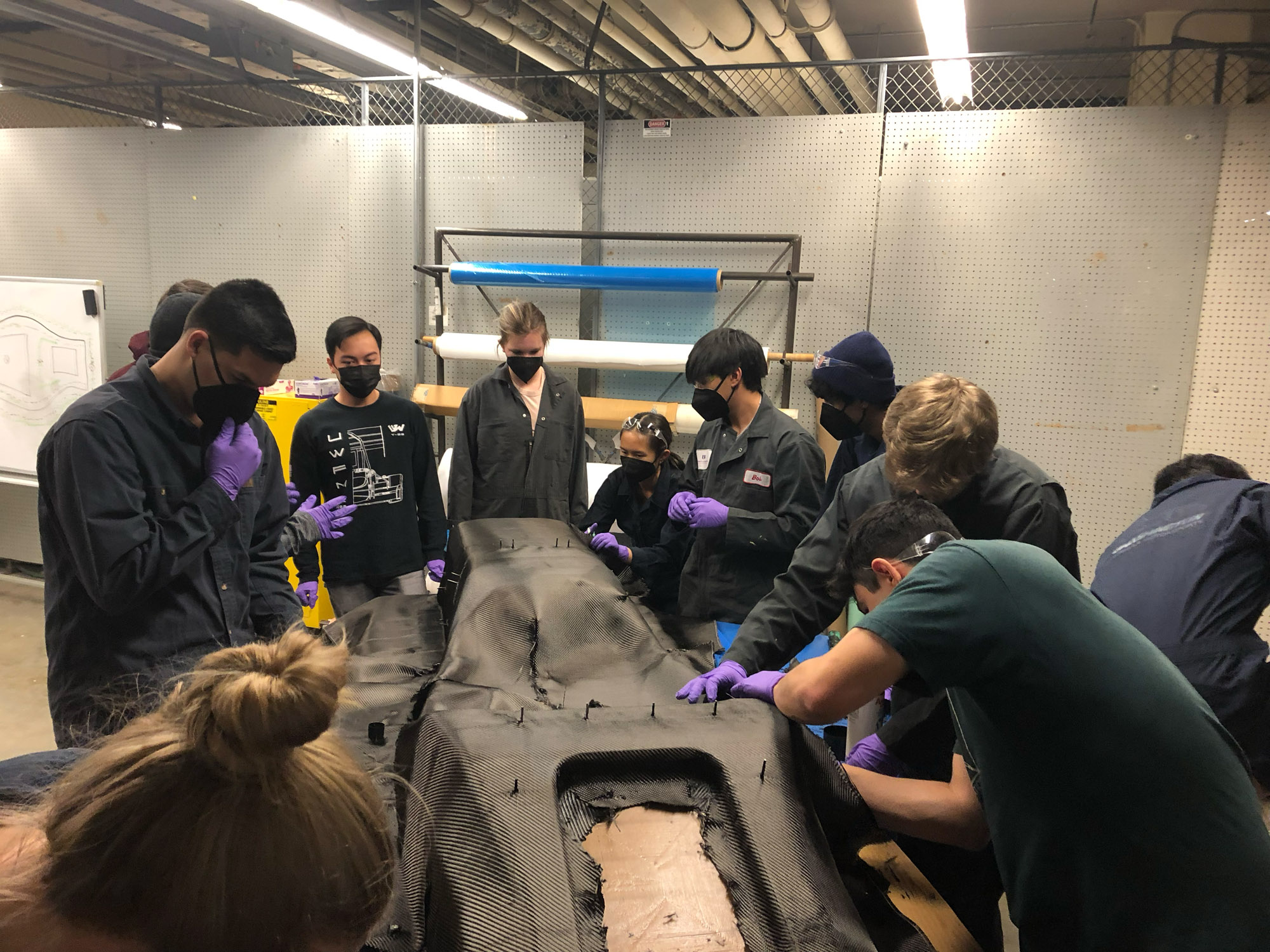
Chassis designs and manufactures the carbon fiber composite monocoque, the foundation of our vehicle. As the main structural component, Chassis team works with all technical teams in order to integrate each system . Additionally, members on Chassis design safety devices such as crash structures such as the roll hoops, and driver interfaces such as the seat. Over the course of the Summer, Chassis goes through extensive design iterations, combining structural analysis, driver ergonomics, vehicle packaging, and functionality, to allow for manufacture through the following year. Care must be taken to comply with competition rules, whilst achieving stiffness specifications, target weight, and manufacturability.
Composites
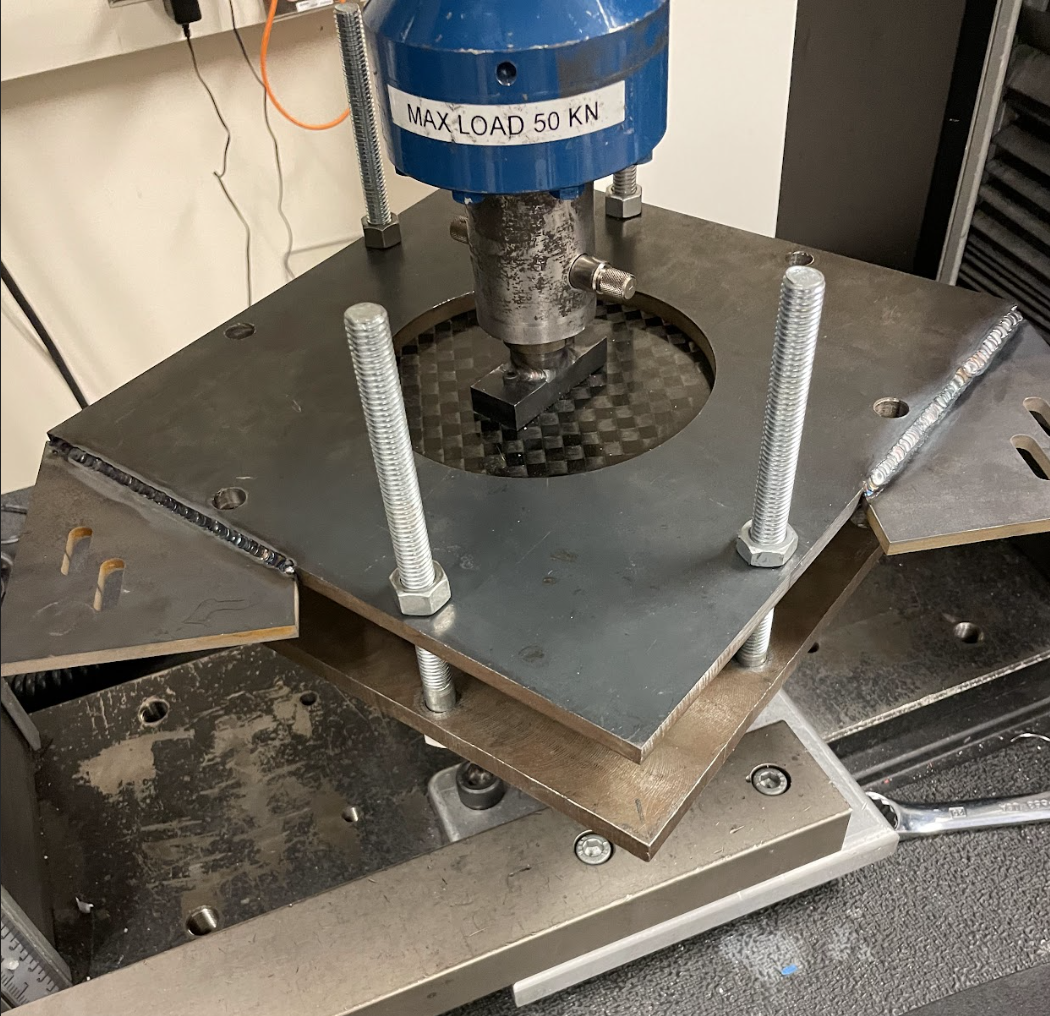
The Composites team is primarily composed of new members to expose them to various methods for constructing and analyzing carbon fiber parts. In order to ensure that each component can withstand the forces that are outlined by other subteams and the SAE rules, extensive testing is required. This team works closely with the Aerodynamics and Chassis subteams to consult on technical projects for ply layup design and for manufacturing best practices. Composites focuses on researching innovative composite applications and proving structural equivalency in the Fall and shifts to fabrication of critical components for the rest of the school year. This is important because the research and testing of parts produced by this team is essential for the validation of the structural components during competition.
Drivetrain
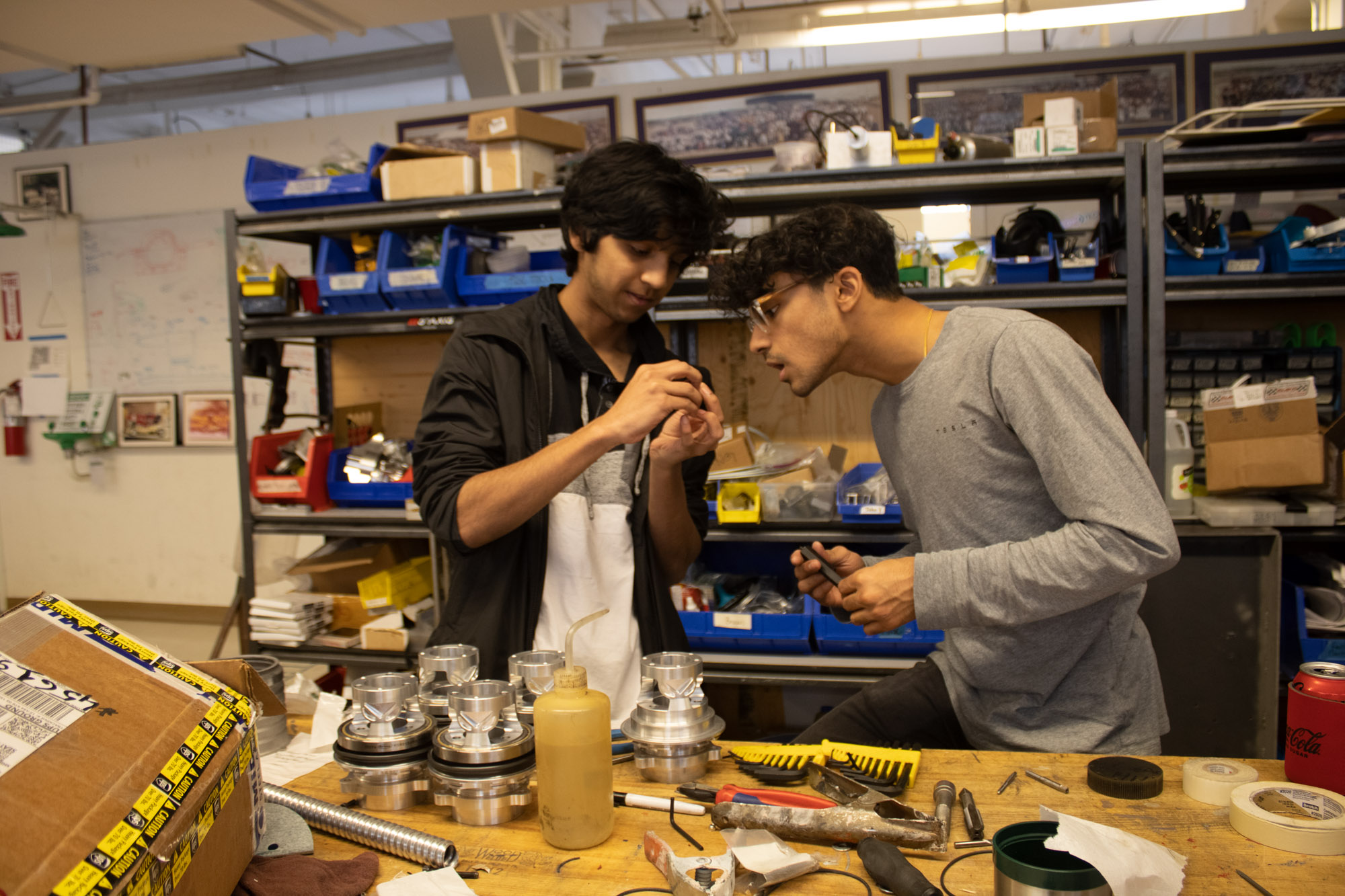
The Drivetrain team is responsible for the design, manufacturing and testing of every component between the electric motor and the wheel. The system contains an ultra high precision compound planetary gearset, laser sintered motor cooling jacket, and a topology optimized titanium suspension upright that doubles as gear housing. As our car follows an in-hub design, a drivetrain assembly is located at each corner of the car. Through the Fall, each member is given a project to refine and improve upon. Drivetrain parts are typically manufactured by sponsors so members will spend the Winter communicating with sponsors to stay on schedule, with the various manufacturing methods ranging from CNC machining to EDM to powder bed printing. At drives, members collect temperature data and monitor wear on various components. Producing a 4WD package that is efficient, reliable, and can operate at peak performance is the main goal of Drivetrain.
Electric powertrain
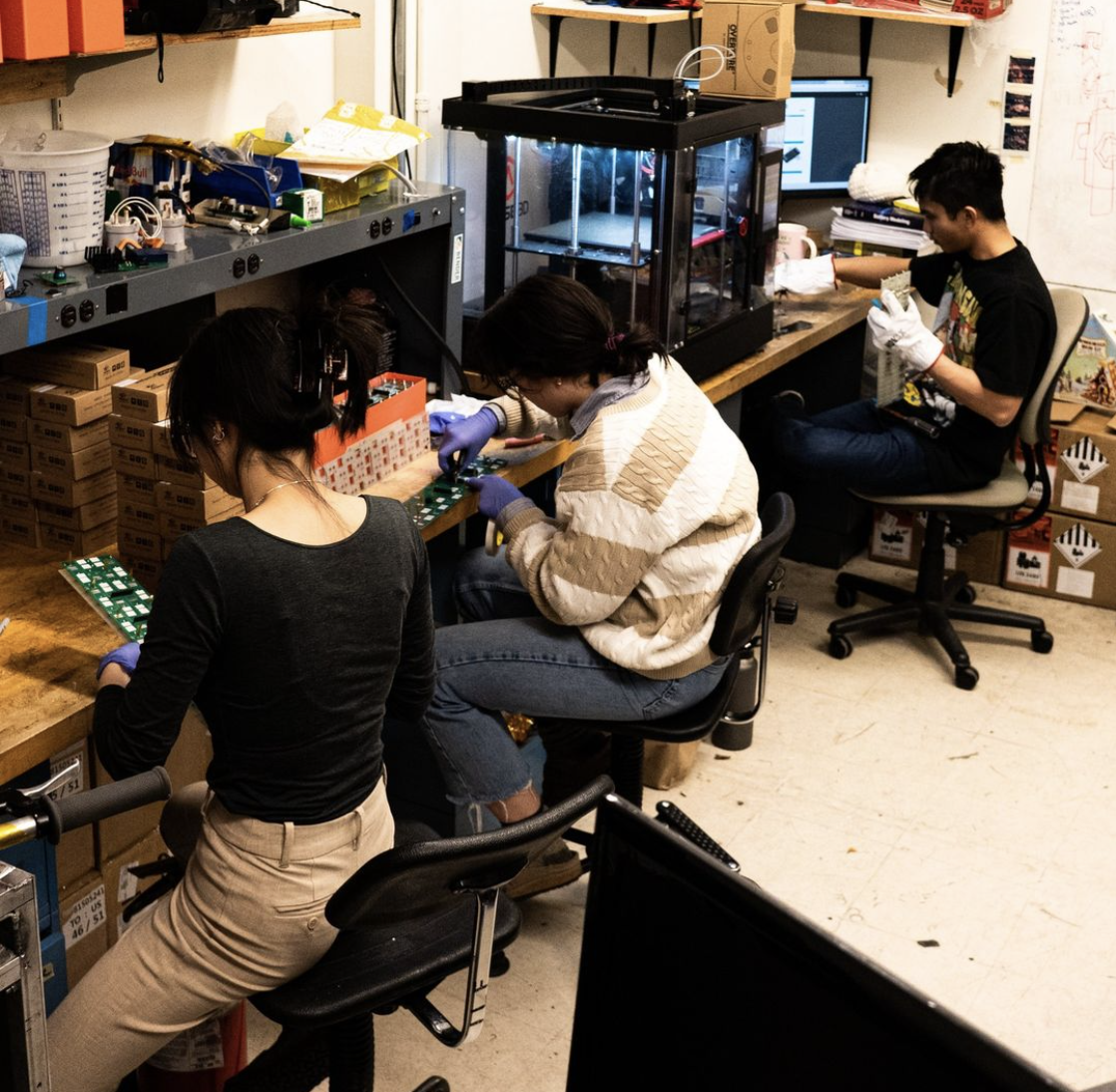
The Electric Powertrain (eTrain) team is responsible for the design, manufacturing, and integration of the high voltage and low voltage battery packs, the inverter packaging, the high voltage junction box, and the high voltage battery pack enclosure. At the beginning of the year, eTrain incorporates data from drives as well as specified performance and rules requirements into the designs of these different projects. In the Winter, eTrain manufactures these components through various methods such as carbon fiber layup, 3D printing, milling, etc. Following the completion of the chassis, electrical integration begins with the incorporation of the battery pack, electronics, and sensors implemented into the car. For the rest of the year, eTrain will work to ensure electrical reliability and durability through testing and debugging.
Manufacturing

The Manufacturing team aids the other tech teams with metalworking and machining of parts while giving newer and less experienced members a solid foundation in manufacturing processes. Understanding how components are manufactured is imperative for designing parts that are both effective and practical. Throughout the year, Manufacturing team members are often tasked with helping other members produce parts or with projects that are necessary for the team to function. These include things such as testing rigs, quickjacks, and many more. The experience gained while on the Manufacturing team is something that can’t be learned in a classroom and gives our newer members the confidence to take on difficult design projects in the future.
Suspension
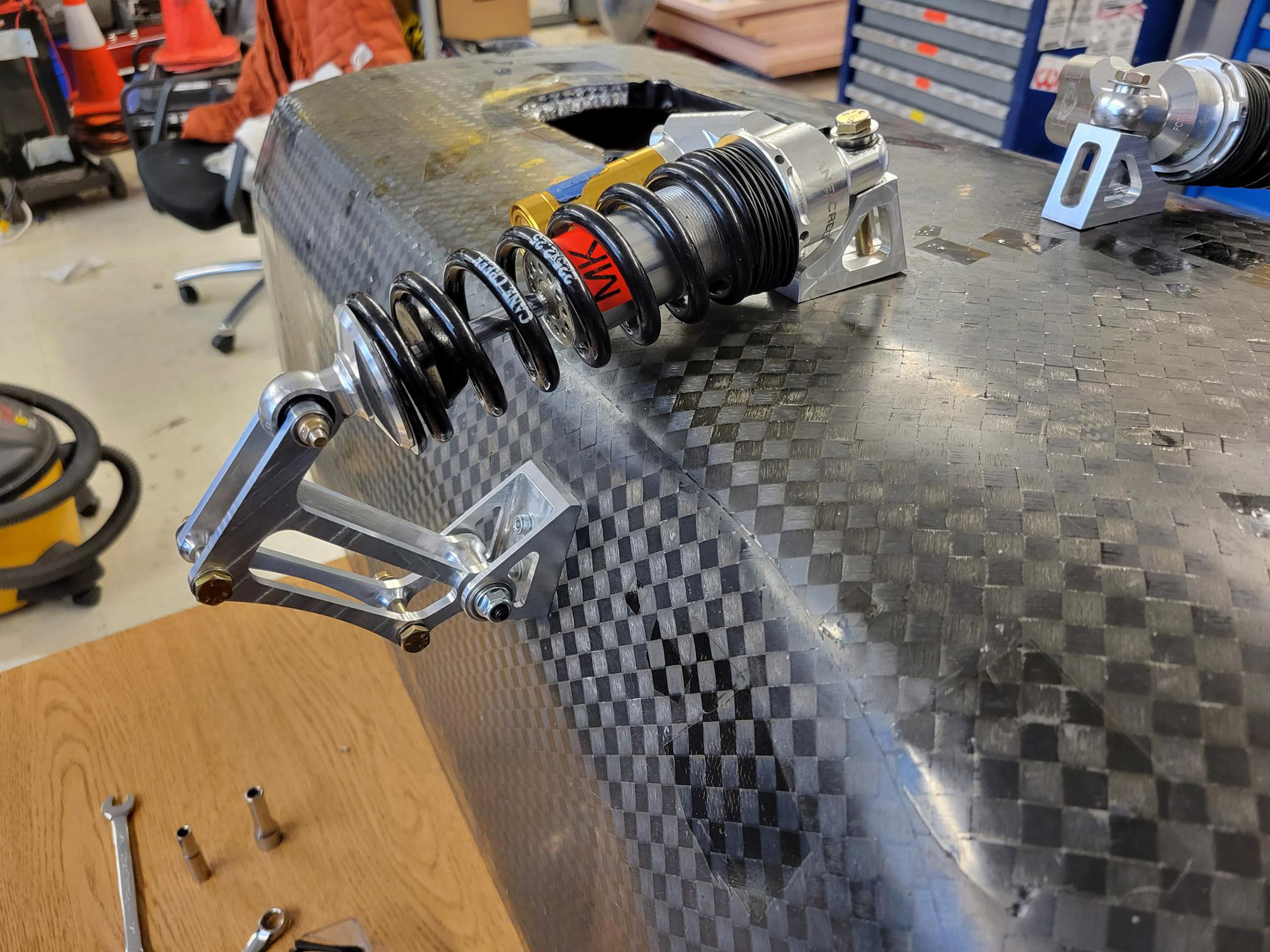
The Suspension team is responsible for increasing mechanical grip between the tires and the track in order to provide steering stability and comfort for the driver. The Suspension team works through the Fall, analyzing drive data to make informed design decisions on various projects such as the control arms, bellcranks, anti-roll bars, steering, and brakes. Through Winter quarter, various components are manufactured in-house as the team works towards the rolling chassis. Rolling chassis is the mounting assembly of all suspension components onto the completed monocoque, thus marking the first major milestone of the team each year. Following the integration of all electrical systems, aerodynamics, and driver, the Suspension team takes measurements to confirm ride height and quality. The data collected during drives is then analyzed, along with the driver feedback, to tune and refine the suspension components and produce a balanced and stable race car.